Fidèle à la marque Anycubic avec ma Kobra 2 depuis plusieurs années, je viens de faire l’acquisition d’une Kobra 3 Combo.
Par Combo, il faut comprendre qu’il s’agit d’un pack contenant une imprimante Kobra 3 et d’un boitier ACE, qui permet d’accueillir 4 bobines.
Cette solution – à l’heure où j’écris – est à 320 €, ce qui la place loin devant ses concurrentes. Mais est-ce « une bonne affaire » ?
L’aspect mécanique
Donc, d’un côté, vous avez une imprimante avec un « hub » au dessus de la tête d’impression, ce hub permettant de relier 4 tubes PFTE, qui sont reliés au ACE, gros boitier, relativement lourd (vous comprendrez plus tard pourquoi je dis cela), qui permet la gestion de 4 bobines de filament, tout en les maintenant à un température idéale (pour le PLA et l’ABS).
L’ensemble est finalement très volumineux s’il est positionné comme sur la photo ( et il ne faut pas oublier qu’il est possible de gérer un deuxième ACE, pour imprimer avec 8 bobines) .
De nombreux utilisateurs ont décidé de positionner ce ACE au-dessus de l’imprimante, comme ce qui est fait par des produits concurrents, ce qui donne une installation de ce genre :
Alors, honnêtement, je pense que c’est une fausse bonne idée, et ce, pour plusieurs raisons.
D’accord, on gagne de la place sur le bureau mais :
- je l’ai déjà dit, le ACE est « lourd »,
- l’imprimante « vibre » énormément, surtout en mode Sport,
- le centre de gravité se retrouve très haut, et le risque de basculement n’est pas négligeable.
Mais cela fonctionne visiblement !
J’ai personnellement opté pour une autre solution : mettre le ACE en dessous de l’imprimante.
Ayant l’habitude de plutôt travailler debout, j’avais déjà surélevé ma Kobra 2, ce qui m’avait permis de mettre un boitier de séchage bobine en dessous.
J’ai donc naturellement appliqué ce même choix pour ma Kobra 3.
Côté tubes PFTE, ils sont assez longs pour que cela ne pose pas de problème fonctionnel, même lorsque la tête est en position haute.
Et pour l’accès au boitier ACE, 2 glissières de tiroir permettent de le sortir totalement …
L’aspect fonctionnel
Maintenant que l’imprimante est installée et est fonctionnelle, et avant de détailler comment on va imprimer en plusieurs couleurs, il est important d’avoir une idée du fonctionnement de cette imprimante !
Il va y avoir exclusivement 2 types d’impression multi-couleurs : soit les couleurs sont réparties dans le modèle (image de gauche), soit les changements de couleur sont répartis en couches (image de droite).
La Kobra 3 dispose d’une tête unique sur laquelle est connecté un Hub 4 voies. Le mécanisme d’impression « en couleur » est donc le suivant :
- le ACE introduit le filament de départ,
- l’imprimante « purge » la tête d’un volume déterminé,
- l’impression commence, jusqu’au changement de couleur programmé,
- l’imprimante « coupe » le filament,
- le ACE rétracte le filament (et le rembobine), puis introduit le filament,
- etc.
Le cycle se reproduit ainsi jusqu’à la fin de l’impression.
A chaque changement de couleur, la machine génère un déchet de purge.
Lorsque l’on imprime une pièce avec des changements de couleur par couche (comme le dyno de droite), les déchets restent limités. Mais si l’on imprime des pièces qui présentent plusieurs couleurs sur de mêmes couches, il faudra s’attendre à avoir un volume de déchets non négligeable par rapport au filament utile à la pièce. A noter aussi que le temps d’impression sera sérieusement rallongé.
En résumé : si vous imprimez majoritairement des pièces multi-colorées, passez votre chemin ! Il faudra privilégier une imprimante multi-têtes, qui ne générera pas de déchet. Par exemple, la Prusa XL ….
Mais il vous faudra, dans cette configuration 5 Têtes, débourser 3700 €, soit un peu plus de 10 fois le prix de ma Kobra 3 !!!
L’aspect tranchage
Pour préparer les fichiers, Anycubic met à disposition son propre Slicer, nommé « Anycubic Slicer Next ».
C’est à ce jour, le seul slicer qui prends en compte nativement le ou les 2 Aces connectés à la Kobra 3. Si en plus, les bobines de filament sont équipés d’une puce RFID compatible (cela fera l’objet d’un autre article), les caractéristiques des filaments seront directement remontées dans le slicer.
Concernant le paramétrage en lui-même, pas de révolution par rapport aux slicers « classiques » comme PrusaSlicer ou Orca.
Le mode opératoire est classique :
a) on charge le modèle à imprimer :
ici un petit requin articulé déjà prévu en 3 couleurs.
Dans l’onglet « Préparer » on va pouvoir ajuster les paramètres d’impression comme dans n’importe quel slicer. A ce stade, on peut aussi « peindre » la pièce, c’est à dire définir quel filament utiliser à tel endroit.
Une fois l’option sélectionnée, je choisis le filament, le type d’outil, et je clique sur la zone à « peindre ». J’ai ici personnalisé mon requin (dans une config qui va générer pas mal de déchets, car je vais avoir des couches avec 3 couleurs, donc 3 cycles de purge).
b) on tranche le modèle
Ici un exemple d’une couche « couteuse » en temps et en filament :
impression du noir puis purge puis impression du blanc puis purge puis impression du rouge puis purge puis impression du bleu. Et cela répété à chaque couche de cette nature !
c) on sauvegarde le gcode, ou on l’envoie directement à l’imprimante
La Kobra 3 dispose d’une connexion réseau. Il est donc possible directement d’envoyer le fichier en impression.
Il est alors encore possible de modifier les couleurs globales de la pièce (on décide d’inverser 2 couleurs, ou de changer de bobine de filament). Je peux aussi décider de faire un nivellement automatique du plateau avant l’impression (ou d’autres opérations).
Une fois l’impression lancée, on peux suivre l’impression (et oui, la Kobra 3 Combo est livrée avec une caméra). Il est aussi possible de modifier les paramètres de température de la buse, du plateau, du ACE.
Ensuite, il n’a y plus qu’à attendre, et dans sa catégorie, elle fait le job, avec une belle qualité d’impression.
Un bon investissement alors la Kobra 3 Combo ?
Mon avis est que pour le prix, le résultat est quand même bluffant. Alors d’accord, on génère des déchets et on rallonge les temps d’impression. Mais en comparaison tu temps passé à préparer et à peindre une pièce, cela n’est pas grand chose. Et puis, l’usage n’est pas « toujours » à l’impression multi-couleur : il y a aussi un usage de changement de couleur par couche, comme dans le cas des impressions HueForge (cela aussi fera l’objet d’un prochain article).
Et personnellement, j’apprécie d’avoir toujours à disposition 4 couleurs différentes à choisir au moment de l’impression, lorsque j’imprime un modèle mono-couleur.
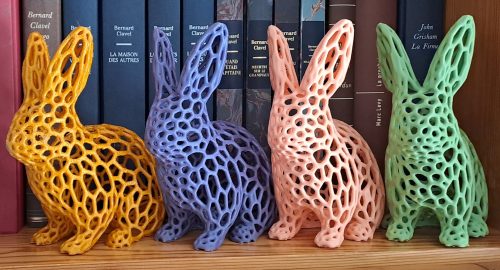
Donc, ma réponse est oui. Pour le prix, vous ne trouverez pas mieux !
Ce qu’il est possible d’améliorer
1) la stabilité
c’est certainement la première chose à faire ! La Kobra 3 est rapide. En mode « Sport », elle a même tendance à terriblement vibrer. Il est donc important à mon sens de tenter d’amortir au maximum les vibrations engendrées. Personnellement, j’ai choisi de monter mon imprimante sur des tampons amortisseurs imprimés en TPU, et fixé sur le plan de travail.
Une bonne assurance pour moi que ma Kobra 3 ne terminera pas sa course quelques mètres plus bas. Vous trouverez différents modèles sur le net.
2) récupération des déchets
Comme décris précédemment, l’imprimante génère tout un tas de petits déchets (je vais voir si je peux en faire quelques chose dans un autre article). Ces déchets sont éjectés sur la partie droite de l’imprimante. Une évolution utile consiste à diriger ces rejets dans un bac . Ubne fois encore, il existe de nombreux modèles dispo sur la toile. J’ai perso retenu un modèle très simple qui renvoie simplement vers le bas, dans un récipient les déchets.
Un système à améliorer car quand la tête est très haute, tout ne tombe pas toujours dans mon récupérateur !!!
3) se passer du ACE
Le ACE, c’est bien, mais il a ses limites. Il n’accepte pas le TPU par exemple. Et si, pour une impression, on a besoin ponctuellement de ce type de filament, il faut enlever un PFTE, et alimenter la tête manuellement. Heureusement, encore une fois sur plusieurs sites, on peux trouver des designs de HUB modifiés. Pour ma part, j’ai opté pour un HUB 5 voies, utilisant des connecteurs ECAS04, connecteurs standard pour les tubes PFTE.
J’ai donc maintenant la possibilité soit d’utiliser le ACE avec ses 4 bobines, soit d’utiliser une bobine externe, et ce, sans avoir à démonter quoique ce soit !
Et pour terminer
Sachez qu’il est possible d’acheter la Kobra 3 seule, le ACE seul, qu’il existe un modèle Kobra 3 Max (avec un plus grand volume d’impression) et qu’un kit de migration de la Kobra 3 vers Kobra 3 Max est annoncé !
Sur le site officiel de Anycubic, vous trouverez aussi la Kobra S1 Combo, imprimante avec enceinte de protection et ACE, qui ressemble comme 2 gouttes d’eau à une de ces concurrentes que je ne nommerais pas.
A vous de décider maintenant.