Je ne vais pas vous mentir, je suis un utilisateur définitif de FreeCAD !!!
Mais je rencontre des personnes qui commencent dans la modélisation et qui sont séduites par Fusion 360.
Je vais donc tenter de faire un petit comparatif entre ces 2 produits, qui ont certainement leurs avantages et leurs inconvénients.
Un premier constat
Avant de commencer un comparatif « fonctionnel », il est important de savoir ce que l’on va comparer.
Côté FreeCAD :
- un logiciel totalement open-source,
- de nombreuses fonctionnalités sous forme d’ateliers à ajouter, issus d’une communauté très active,
- installation et utilisation en local.
Côté Fusion 360 :
- un logiciel qui nécessite la création d’un compte, qui même si l’on travaille avec la version gratuite, doit être renouvelé tous les 3 ans,
- une version gratuite « bridée »,
- installation en local, mais nécessité d’avoir un accès internet pour l’identification et le stockage en Cloud.
Rien qu’en écrivant les mots « Compte », « bridée » et « Cloud », je suis déjà conforté par mon choix pour FreeCAD, et son aspect « libre ».
Néanmoins, comme nous allons le voir rapidement, et à périmètre équivalent, Fusion 360 va être plus simple à prendre en main pour quelqu’un qui débute, car ses menus sont très certainement mieux pensés que FreeCAD.
Dans la suite de cet article, je vais donc tenter, par des exemples de plus en plus complexes, de réaliser d’abord la conception sous Fusion 360, puis sous FreeCAD. Vous devriez constater que – dans la plupart des cas – la philosophie de conception reste la même.
Remarque :
Quelle que soit la pièce que vous souhaitez réaliser, quel que soit l’outil que vous allez utiliser, il est primordial de commencer pas se poser une simple question : « Comment est faite cette pièce ? ».
Cela vous évitera de vous lancer dans une conception complexe, alors qu’une solution plus simple pouvait exister.
Cas n° 1 : une rondelle
Quoi de plus simple qu’une rondelle. Et pourtant, on va déjà pouvoir constater qu’il va exister plusieurs façons de la concevoir.
Une rondelle, c’est « un cercle que l’on extrude pour ensuite y percer un trou » ou « 2 cercles concentriques que l’on va extruder » ou « un rectangle sur lequel on applique une révolution ». J’avoue la dernière solution est u peu tordue.
Mais ces 3 visions vont permettre de rapidement comparer les modes opératoires de FreeCAD et Fusion 360.
Réalisation avec Fusion 360
On sélectionne « Créer une esquisse » puis on sélectionne le plan de travail.
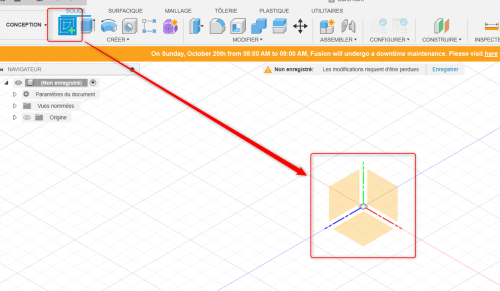
On choisi ensuite l’outil « Cercle ». On dessine au centre un cercle en précisant une dimension de 40 mm. On clique sur « Terminer l’esquisse ».
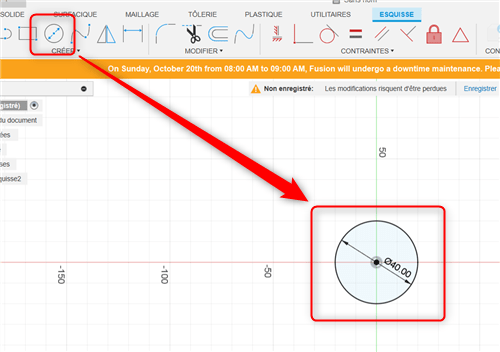
Il reste à « Extruder » la pièce d’une hauteur de 10 mm.
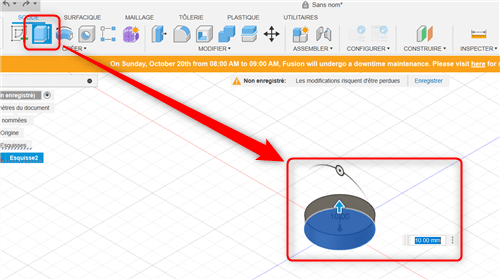
On répète l’opération, en sélectionnant la surface supérieure du cylindre obtenu, en y dessinant un cercle de rayon 15 mm, et en effectuant une extrusion, mais cette fois « négative ».
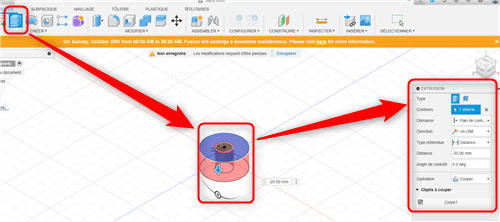
Et on obtient notre rondelle !
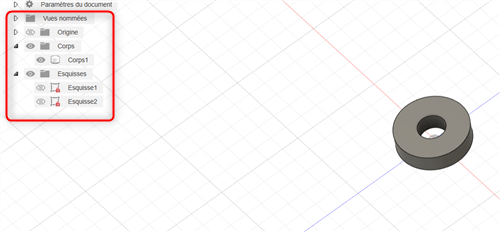
A noter que l’on dispose de l’arborescence du modèle, et qu’il est possible de le reprendre à tout moment.
Réalisation avec FreeCAD
FreeCAD travaillant avec des ateliers, la première chose à faire est de sélectionner l’atelier « Part Design ». Ensuite on crée un nouveau document, puis un « corps » puis une « esquisse ». Il suffit en fait de suivre ce que propose FreeCad. On arrive alors sur un écran de choix de plan.

Comme avec Fusion 360, vous choisissez le plan sur lequel vous souhaitez travailler.
Comme dans Fusion, on sélectionne l’outil « Cercle », on dessine un cercle au centre. On sélectionne ensuite l’outil « Diamètre » et on applique un diamètre de 40 mm au cercle. Puis on ferme l’esquisse.
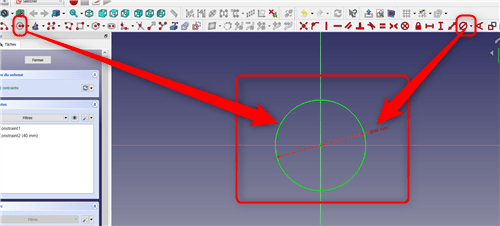
On applique ensuite une « extrusion » de 10 mm à l’esquisse que l’on vient de dessiner.
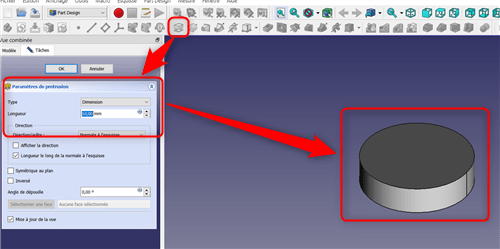
On répète de même pour le trou : on sélectionne la face supérieure, on créé une nouvelle esquisse, on y place un cercle de 15 mm.
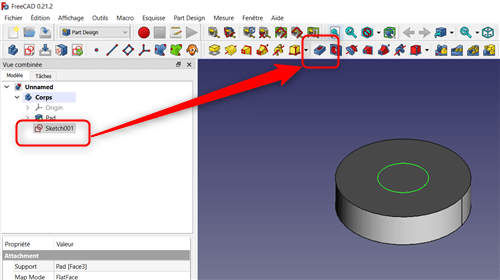
On va cette fois utiliser l’outil « cavité » pour créer le « trou ». Nous obtenons notre rondelle.
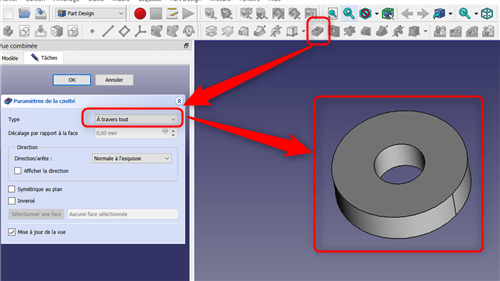
Sur la réalisation de ce type de pièce, l’utilisation de Fusion 360 ou de FreeCAD ne sera finalement qu’une question de choix et d’habitude, et ce, quelle que soit la méthode de conception. On retrouvera sur les 2 logiciels les mêmes outils et fonctionnalités.
Cas n° 2 : Réalisation d’une vis
Je vais volontairement prendre cet exemple, car il va illustrer parfaitement une grande différence entre les 2 logiciels.
Mon objectif : réaliser une vis de fixation à tête hexagonale M8 x 40 (diamètre 8, longueur 40) conforme à la norme ISO 4017 (soit une longueur de tige entièrement filetée).
Réalisation avec Fusion 360
On sélectionne « créer », puis « polygone », « polygone circonscrit ». Et on dessine un polygone de 6,5 mm (puisqu’une tête M8 hexagonale fait 13 mm de largeur).
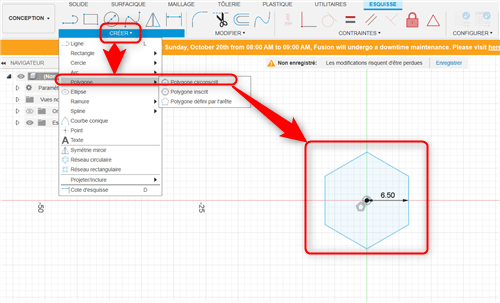
Je termine l’esquisse et je l’extrude de 5,3 mm (hauteur de tête normalisée).
Je dessine une nouvelle esquisse avec un cercle de 8 mm, que j’extrude à son tour sur une hauteur de 40 mm.
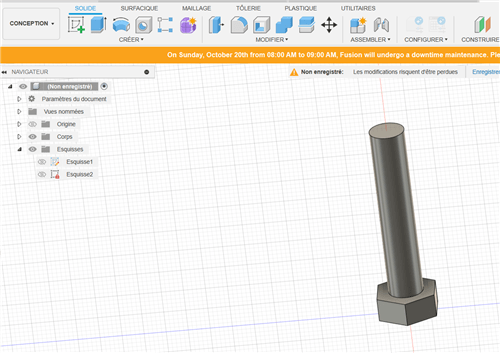
Fusion 360 dispose d’un outil « Filetage », qu’il suffit d’appliquer sur la surface cible.
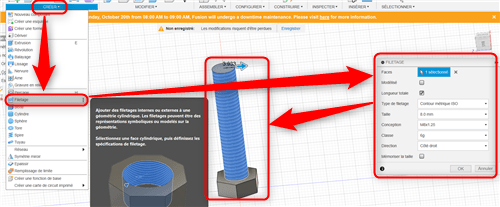
Notre vis est presque terminée.
Il reste à générer des chanfreins en bout de vis et sur la tête.
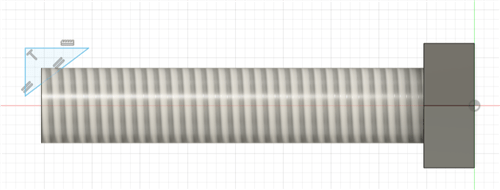
Je fais cela en dessinant une esquisse triangulaire à laquelle j’applique une révolution de 360° autour de l’axe de la vis, en « soustraction de matière ». La même opération est à réaliser côté tête.
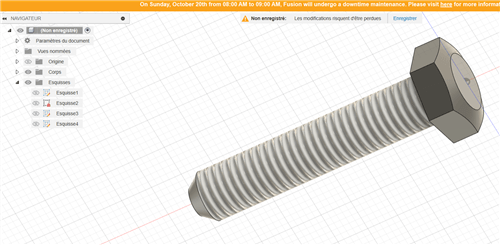
Voici une belle vis, réalisée sous Fusion 360, en seulement … 4 esquisses.
Réalisation avec FreeCAD
C’est ici que l’on voit la puissance des ateliers ! J’ouvre l’atelier « Fasterners ».
Il me propose directement d’ajouter une vis à la norme ISO 4017, pour laquelle il suffira de définir le diamètre (M8) et la longueur (40), le tout en une étape !
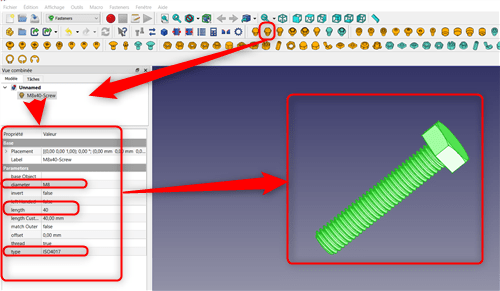
Le principal intérêt est ici que si je souhaite modifier le diamètre de ma vis (parce que j’aurais mal fais mon choix et que je m’en aperçois dans un assemblage), il suffira de modifier la valeur M8, pour que tous les paramètres de la vis soient modifiés (taille de la tête en particulier).
Avec la conception sous Fusion, il faudra que j’intervienne sur plusieurs esquisses.
Besoin de plan 2D ?
L’un des besoins possibles lors d’une conception est de pouvoir générer des plans 2D côtés. En effet, une pièce ne sera pas nécessairement « imprimée » mais pourra nécessiter un usinage par un tiers (si je voulais faire ma rondelle en aluminium par exemple). Regardons ce que proposent nativement Fusion et FreeCAD.
Côté Fusion 360
Reprenons notre vis M8x40. Fusion 360 propose un menu « Dessin ».
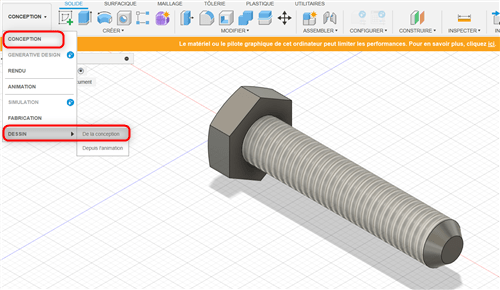
En sélectionnant l’option, on arrive sur le menu suivant :
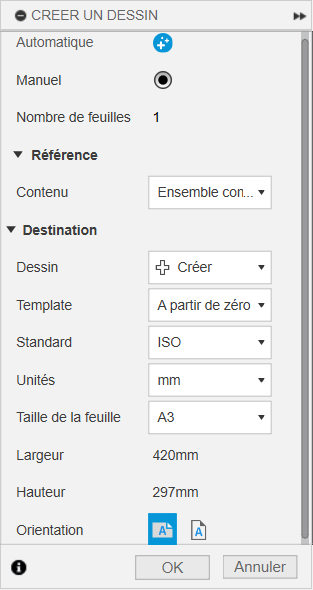
Le mode « Automatique » est payant ! L’utilisation de template est payant !
On va donc se contenter du minimum, à savoir créer le dessin sur un doc A4 en paysage, en ne changeant aucune autre option.
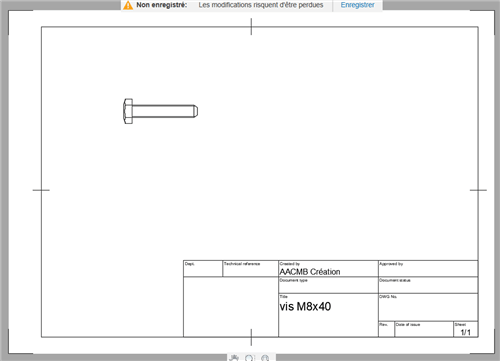
Fusion 360 me génère donc une feuille A4 comme demandée, en me proposant de placer une vue de la pièce. C’est plutôt une approche sympa.
Nous disposons ensuite de différents outils pour rajouter des vues.
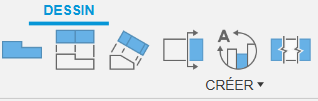
Si vous avez choisi un dessin à la norme ISO, les vues sont positionnées selon la norme : La vue de gauche est placée à droite, celle de dessus en dessous. Ici , j’ai rajouté la vue de gauche et une vue en perspective.
Une fois les vues positionner, Fusion 360 met à notre disposition un ensemble d’outils pour réaliser la cotation.

On arrive facilement à un résultat correct.
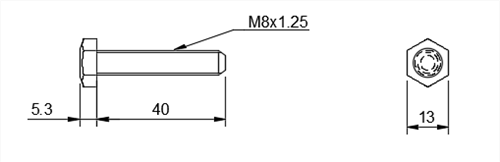
Malheureusement, les options d’exportation sont payantes. Seule solution, imprimer au format pdf.
Côté FreeCAD
FreeCAD dispose de l’atelier « TechDraw », spécialisé dans les plans 2D. La première opération à réaliser est d’ajouter une page à notre modèle. 2 options sont possibles :

Soit on insère une page par défaut (icône de gauche). Cette page est définie dans le paramétrage de l’atelier. Soit on utilise l’icône de droite, qui permet de choisir un template (inclus par défaut). Ci-dessous un exemple non exhaustif.
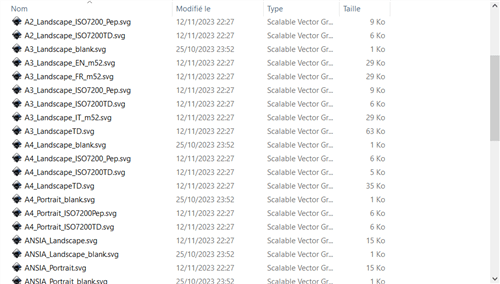
Une fois le template choisi, on obtient une page blanche dans laquelle il va falloir ajouter les vues désirées. FreCAD permet l’ajout de différentes façons.
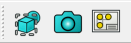
De gauche à droite ; insérer une vue unique, insérer une capture, insérer un groupe normalisé. C’est cette option qui reste la plus utile à mon sens, dans un premier temps.
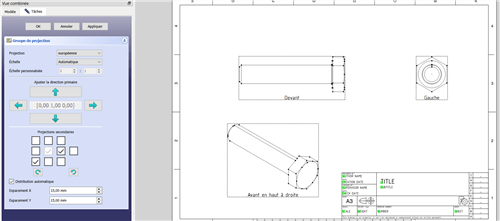
D’un usage plus simple que Fusion, on va pouvoir choisir en « live » les vues et projections que l’on souhaite faire apparaitre. A noter aussi que l’on pourra choisir un mode d’échelle automatique pour que la représentation occupe au mieux l’espace de la feuille.
Il reste ensuite à coter la pièce, avec les outils disponibles. On reste ici dans la même phylosophie qu’avec Fusion 360.
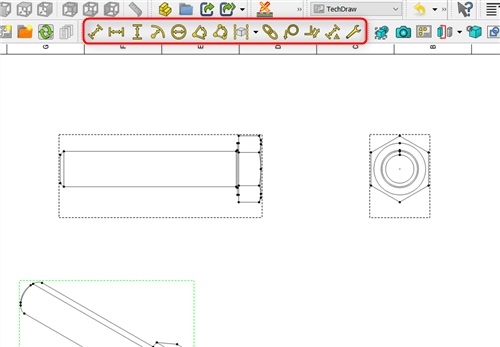
On arrive aussi à un résultat satisfaisant :
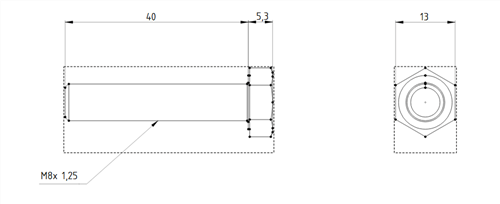
En conclusion
2 logiciels qui vont vous permettre d’arriver à vos fins. Le choix entre les 2 reste à mon sens très arbitraire. Entre un logiciel très ergonomique (Fusion 360) mais payant sur certaines options, et un logiciel entièrement gratuit (FreeCAD) mais un peu plus difficile d’appréhension en raison de l’organisation en ateliers, il seule chose est certaine : il faudra vous tenir à votre choix, ne serait-ce que pour acquérir les automatismes qui vous permettrons d’aller plus vite dans vos conceptions.
Enfin, c’est mon avis …