C’est parce que toutes nos conceptions ne vont pas forcément être imprimées en 3D, il va être parfois nécessaire de pouvoir disposer d’un « plan » à l’ancienne, qui donne une représentation en 2D de la pièce, vue de face, de côté, de dessus, avec des côtes.
Je prendrais par exemple un petit boitier que j’ai besoin de réaliser, et pour lequel je souhaite une face avant en aluminium.
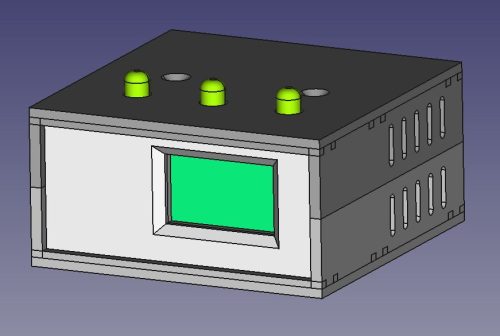
Je vais donc devoir réaliser un plan de ma face avant, avec les côtes nécessaires à sa réalisation. C’est ici qu’intervient l’atelier TechDraw.
Prise en main
Après avoir conçu la pièce, il suffit d’ouvrir l’atelier TechDraw. Un nouveau menu apparait, menu qui va nous permettre de réaliser les opérations suivantes :
- création d’un nouveau document, à partir d’un template normalisé,
- ajout des vues souhaitées,
- mise en place des cotations.
Selon le template, on pourra être amené à effectuer d’autres opérations, comme par exemple, remplir un cartouche.
Création d’un nouveau document
Les icônes pouvant être disposées de manière différente, je passerais par les menus (mais vous pouvez utiliser les icônes, une fois que vous les aurez identifiées ).
On commence donc par créer un document contenant au moins une page.
FreeCAD est fourni avec de nombreux modèles. Pour la démo, je choisi un modèle A4 paysage, qui va comporter un cartouche normalisé (cela va rappeler des bons ou mauvais souvenirs à ceux qui ont suivi une formation de dessin technique).
Nous disposons maintenant dans FreeCAD d’un document prêt à accueillir notre dessin 2D !
Ajout de la (ou des) vue(s)
Avant toute chose, il est nécessaire de se positionner sur la vue que l’on va considérer comme principale. Si cette opération n’est pas réalisée, le résultat ne sera pas « conforme » au besoin. Je vais donc choisir comme vue principale la vue « BAS », qui représente ma pièce de face (c’est empirique et cela dépend de la manière et du plan de base retenu lors de la phase de conception).
Une fois ma pièce sélectionnée, la manière la plus naturelle est de passer par « l’insertion d’un groupe de projection ».
Cette notion de groupe de projection va permettre d’obtenir rapidement une représentation en 2D de votre pièces, sous différentes vues normalisées, que l’on pourra appeler « vue de face », « vue de gauche », « vue de dessus », …
On conservera la représentation « européenne » (qui représente la vue de gauche de la pièce à droite de la vue de face, et celle du dessus en dessous), et comme échelle la feuille (pour que notre représentation tienne sur une page).
Le choix des projections secondaires va permettre de sélectionner les vues utiles à la cotation. Au centre, nous retrouvons la vue initiale de ma pièce, celle sélectionnée tout à l’heure.
Ayant dessiné la pièce, je sais que je vais avoir besoin de préciser des dimensions en regardant la pièce de profil (vue de droite par exemple), et aussi en regardant la pièce par l’arrière.
J’obtiens bien maintenant 3 représentations en 2D de ma pièce, selon les différents points de vue choisis.
Mise en place de la cotation
L’atelier TechDraw offre une palette d’outils permettant la cotation.
Je ne vais pas rentrer dans le détail de chaque outil, le principe restant toujours le même : on sélectionne le ou les points concernés et on sélectionne l’outil (cotation simple, chaine de cotes, diamètre, etc).
L’objectif est d’arriver à définir correctement la pièce. Ci-dessous un début d’exemple.
L’atelier TechDraw va aussi nous donner la possibilité de représenter des pièces en coupe, pour permettre la cotation de zones particulières (ici par exemple la cotation de l’usinage à 45° sur 2 mm dans l’ouverture pour l’afficheur).
Une fois toutes les dimensions correctement renseignées, il nous restera à remplir au besoin le cartouche et à imprimer le document généré, pour obtenir notre plan !
A vous de jouer …